Listen to podcast
20 November 2021 12 Minutes Listen
00:00.00 00:11:55My father is an engineer, and as a young boy, I remember him explaining Moore’s Law to me.
Moore’s Law is named after Gordon Moore, one of the founders of Intel, who in 1965 predicted that the number of transistors on a microchip would double each year. In the years since, Moore’s Law has often been used to illustrate the accelerating pace of technology.
Today, technology continues to grow at an exponential rate and in ever shortened business cycles. Just look at the smartphones we carry in our pockets today – multiple new models are launched every year, each one more powerful than the previous version.
What does this mean for the industrial - in particular the manufacturing - sector, which is heavily dependent on technological advances to drive productivity, efficiency and ultimately output?
For one, it is inevitable that the pace of adaptation and change will increase. It also signals that those working in the sector must continue to advance their skills and knowledge to keep pace with this change, at the same time be the agents of change.
Singapore committed to Industry 4.0
In January this year, Singapore announced its Manufacturing 2030 vision. The goal? To grow its manufacturing sector, currently valued at $106 billion, by 50%. At the same time, manufacturing’s contribution to Singapore’s GDP will be maintained at around 20%.
We hope to undertake this growth through a focused, three-pronged approach: continue investments in the manufacturing ecosystem; build on our existing research capabilities; and promote Industry 4.0 adoption.
What we want to achieve is for Singapore to become a global business, innovation, and talent hub for advanced manufacturing. Our aspiration is for the country to be a place where industrialists can come together and push the boundaries of innovation.
And to meet this target, collaborations ― not only between the private and public sectors, but also among the vertical and horizontal spheres within the private sector ― will be critical.
Building synergistic ecosystems for Industry 4.0 collaborations in Jurong Innovation District
Today, the 600-hectare Jurong Innovation District (JID), master planned and developed by JTC, is home to a growing ecosystem of leading players across the entire industrial value chain.
A beacon for Industry 4.0, JID is a long-term project for JTC and for Singapore. Once mature, it will not only be home to various advanced manufacturers, but also research institutes and capability developers. We have just completed a new phase of our CleanTech Two development, and with the completion of CleanTech Three next year, almost 60,000 sqm worth of space for R&D and collaboration will be added to JID.
We have many committed companies who are already planting their flags at JID. They include Shimano’s factory of the future, as well as Hyundai Motor Group’s Innovation Centre in Singapore. To take advantage of what the district has to offer in the long term, as well as to be the first mover into JID, Hyundai Motor Group is pushing aggressively forward to complete their development in the coming years.
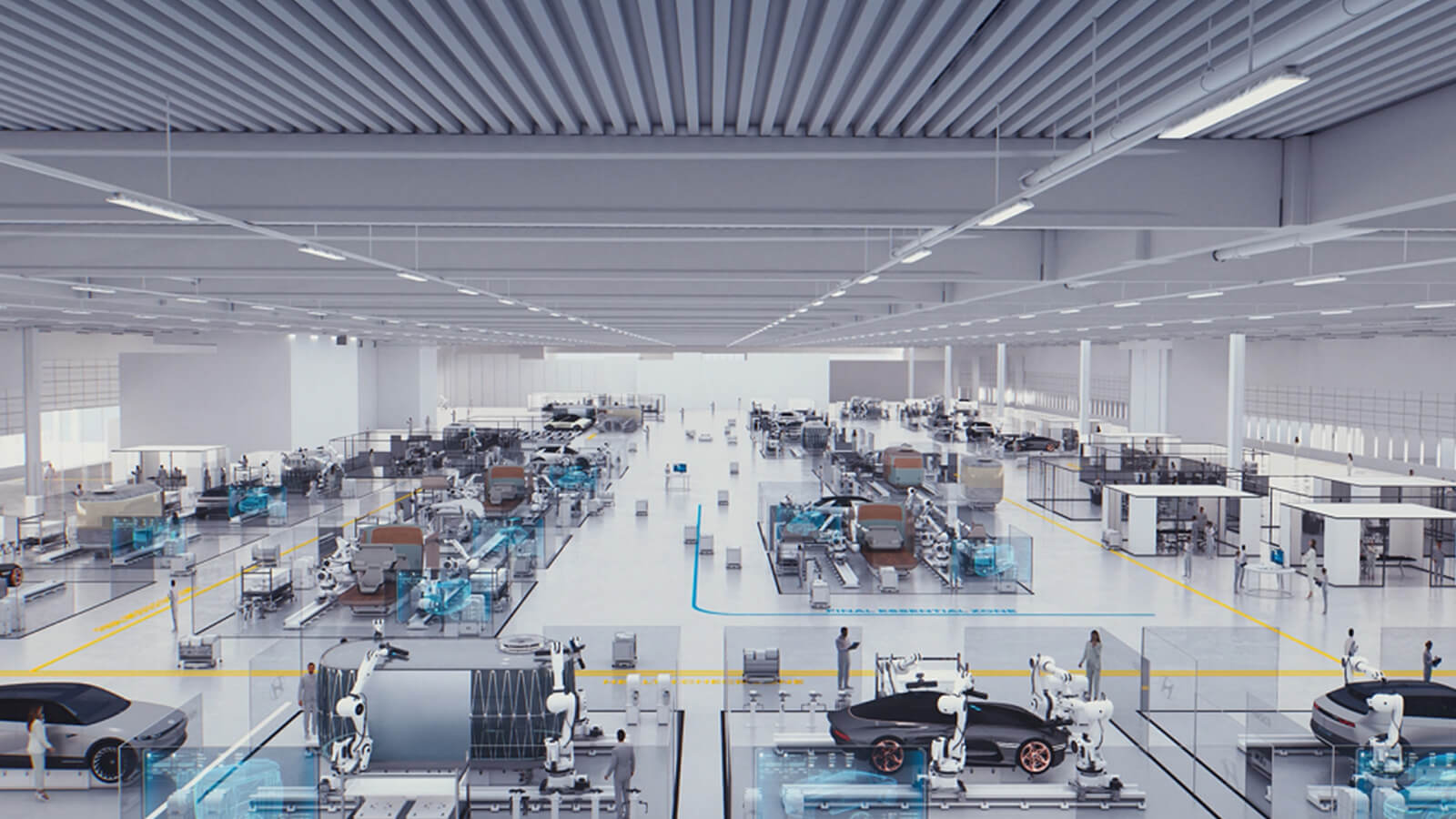
As for research institutes and capability developers, JID already houses Mckinsey’s Digital Capability Centre, as well as the Advanced Remanufacturing and Technology Centre (ARTC), and the Singapore Institute of Manufacturing (SIMTech). The latter two are affiliated to Singapore’s Agency for Science, Technology and Research (A*STAR).
In addition, Industry 4.0 solution providers such as Siemens, Makino, Sodick and Konica Minolta, as well as training providers such as Bosch Rexroth’s Regional Training Centre, and Advanced Manufacturing Training Academy (AMTA), will call JID home. Nanyang Technological University, located right next to the district, will put a pool of talents within reach.
We believe that situating the necessary stakeholders and players within one locality is the first step towards building a unique ecosystem where businesses can innovate and grow, and at a much faster pace. JTC’s traditional role has always been in the real estate sector, but with JID, we believe in going beyond just brick-and-mortar. We want to foster a vibrant community where like-minded partners come together and fulfil Singapore’s Manufacturing 2030 vision with us.
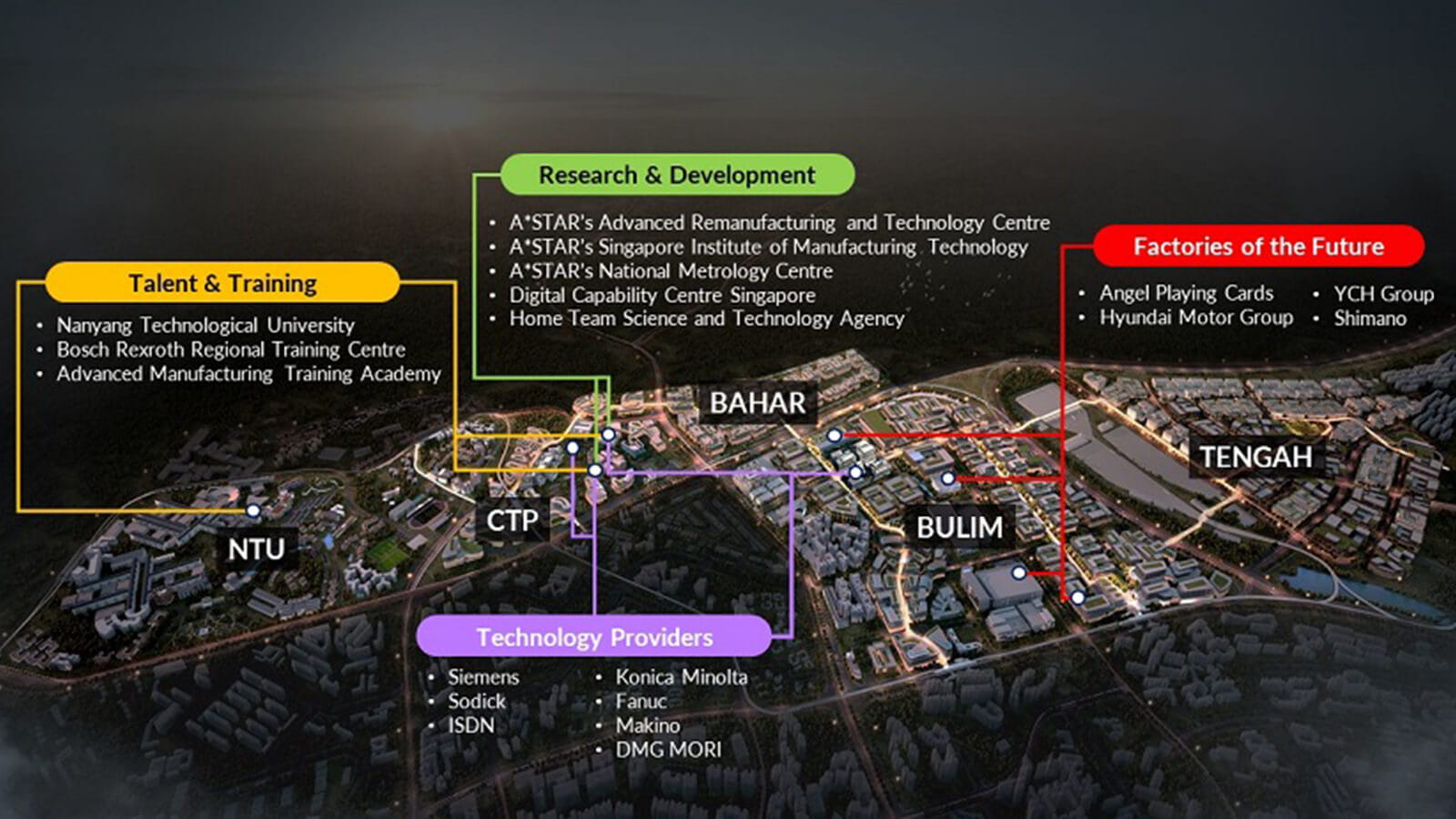
Tapping JID’s ecosystem
Many businesses see the value of partnering global Industry 4.0 solutions leaders to grow their capabilities, and collaborations among partners within JID’s ecosystem have begun to take place.
Flexmech Engineering, a homegrown 37-year-old business supplying precision equipment and services to clients across different sectors around the world, linked up with Bosch Rexroth to create an Industry 4.0 ‘lite’ solution that Flexmech’s clients can use with their machines. Through this, the longevity of the machines are extended, which translates to potential savings of up to $250,000 annually.
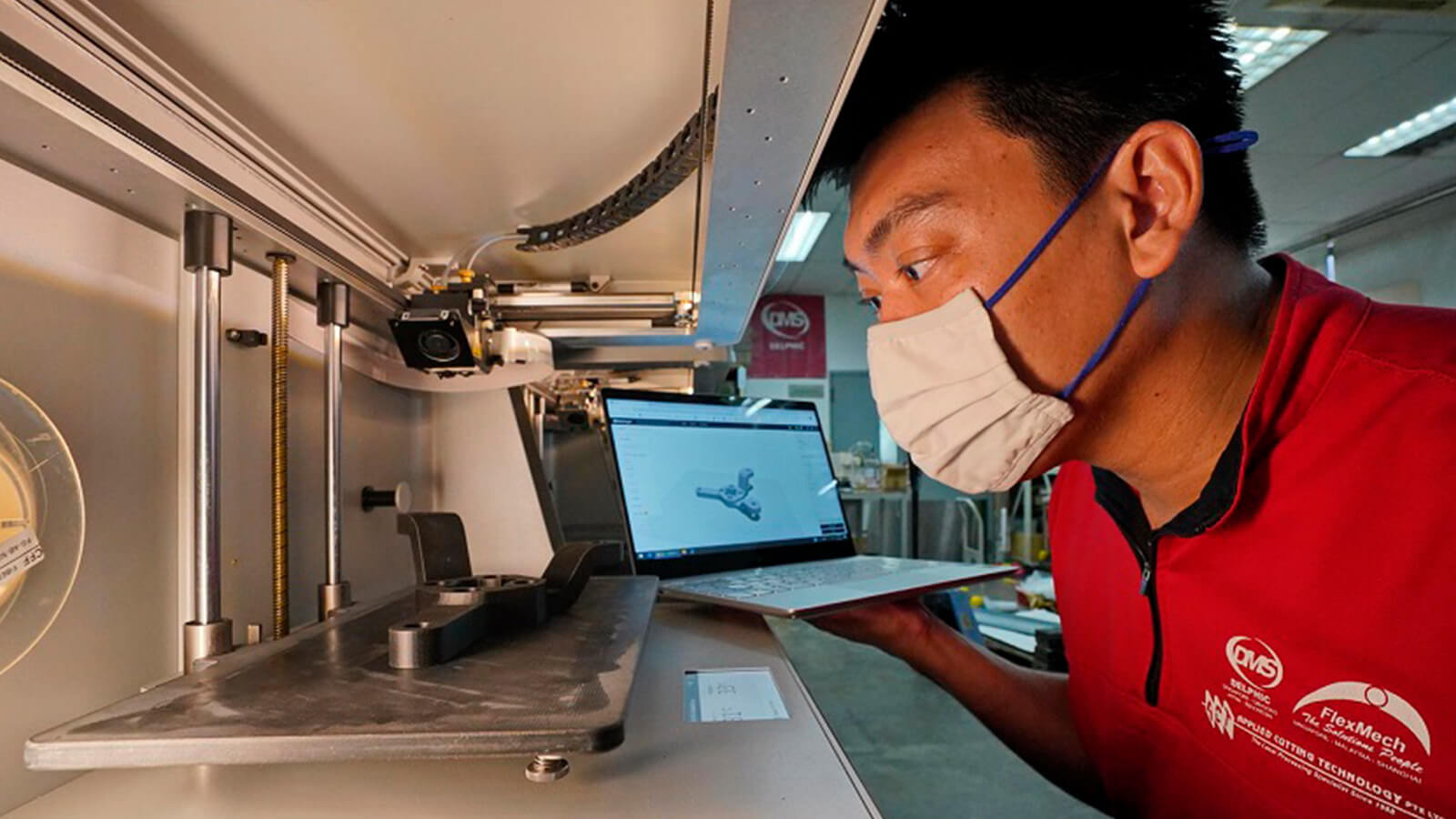
ARTC and Procter and Gamble (P&G) collaborated with local SME JM Vistec to develop an Industry 4.0 solution for SK-II, one of the many well-known brands under P&G. Through this collaboration, an automated inspection system powered by artificial intelligence was created to inspect the glass bottles used in some of SK-II's products. The outcome? The speeds of inspection on the P&G packing line is now three times faster.
Siemens partnered with A*STAR and the National Additive Manufacturing Innovation Cluster (NAMIC) to develop 3D-printed face shields for use on the COVID-19 frontlines. A*STAR helped to develop the final product with the right medical coating; through NAMIC, Siemens connected with partners such as HP and Jabil, who provided the machines and technical expertise required for large-scale 3D printing. Through the partnership, Siemens was able to increase the production of the face shields from 200 to 3,000 pieces each month, with consequential improvements to the design and manufacturing process of the face shields.
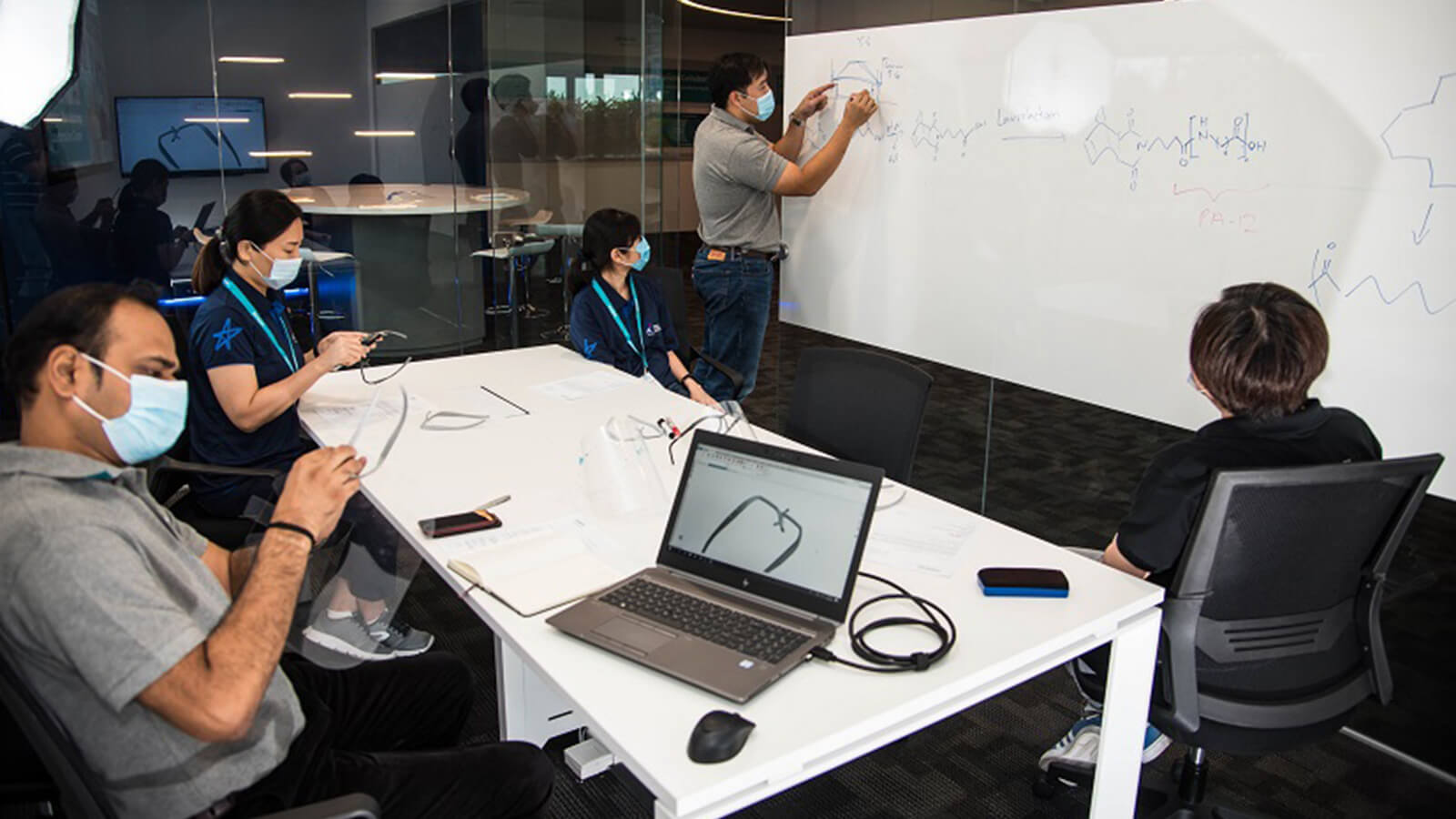
Developing a framework for connections and a mindset for collaboration
These examples show how important it is to develop a framework for connections within the JID ecosystem, and having a mindset of collaboration to achieve common objectives and outcomes. Through our Industry Connect initiative, more than 1,000 businesses in our estates have participated in various Industry 4.0 outreach programmes. Significantly, an estimated 250 SMEs are currently undergoing various phases of digitalisation, transforming their businesses, and turning COVID-19 challenges into opportunities.
I will be the first to admit that it wasn’t easy when we first started this Industry 4.0 journey. Try telling any SME about digitalisation — the first reaction you’ll get is that they think it is expensive and not applicable to small companies. What we need to do then is walk the journey with them, and through various support schemes and grants provided by the government and industry partners, provide them with that edge so that they stay competitive.
After constant engagements and witnessing the various programmes in action, the perceptions of these SMEs slowly changed. Today, many SMEs understand the longer-term benefit of digitalisation and what working with different parties to enhance and improve their productivity can bring. The results? Reduced operating costs, re-designed workflow and processes, and an increase in machine utilisation rate. Productivity is immediately uplifted, leading to higher sales and higher margins.
Interestingly, we have also observed that there is a discernible change once companies transform. Not only are laborious, repetitive, and mundane processes eliminated and replaced, but knowledge is also increased through higher value-added tasks such as data analytics and the operation of high-tech machines. Net-net, this becomes a win for all, with companies and employees benefiting all at once.
Singapore’s manufacturing sector can benefit from a strong talent pipeline. To that end, we have pushed ahead with organising Industry Days such as Biopharma Industry Day, Electronics Day, and Aerospace Day for students. By connecting industry with academia, we hope there will always be a good flow of talents to enrich Singapore’s industrial scene.
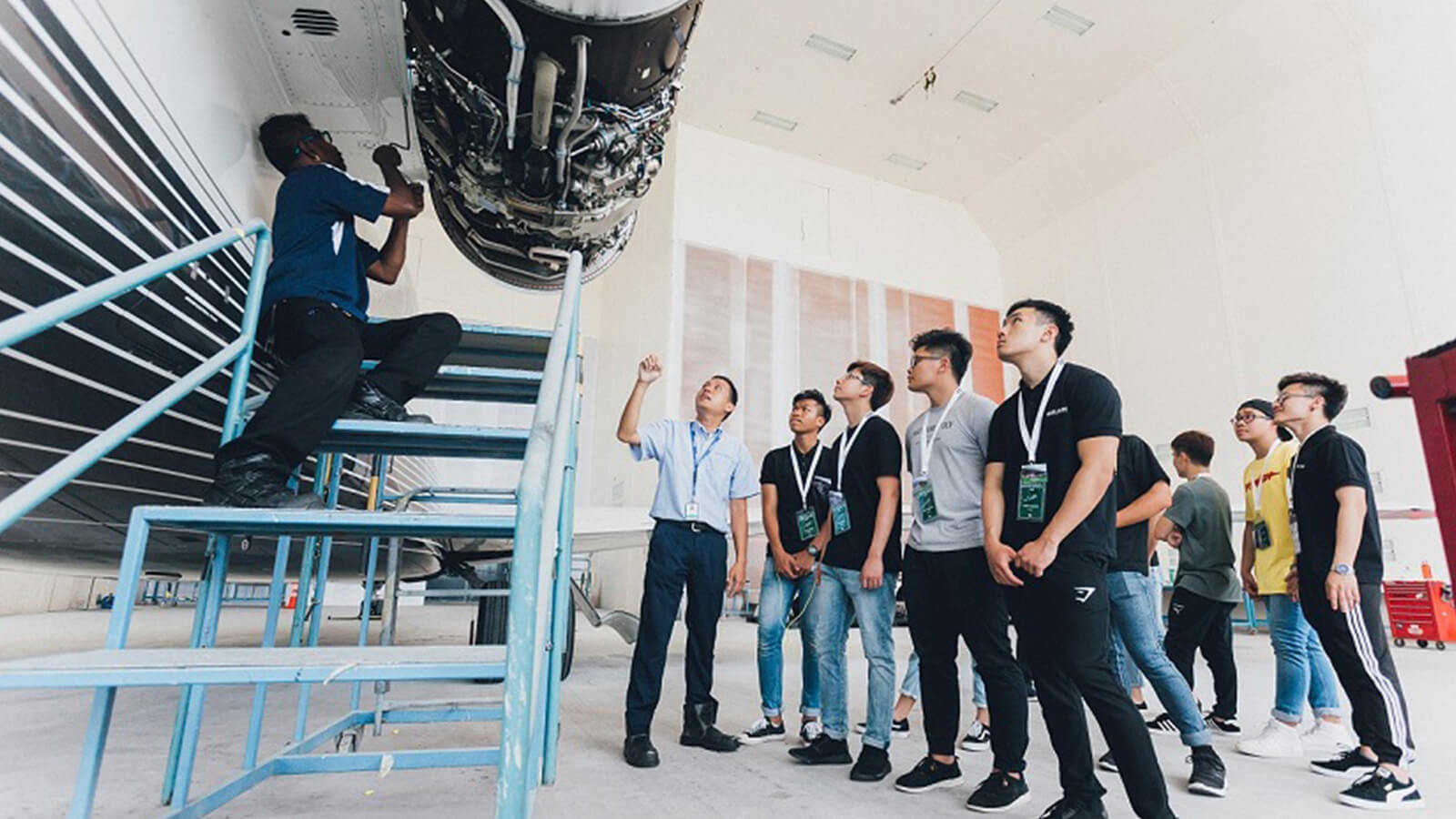
What’s next for JID and Industry 4.0?
Our efforts have only just begun. Moving forward, we will be accelerating our efforts within a more systematic framework. The intention is to help us scale our Industry 4.0 transformation efforts beyond what we are doing now. We have just set up a new Industry Connect Office, and we’re partnering with AMTA to provide consultancy and advisory services on Industry 4.0 skills and training for all. Companies and businesses that are keen to improve or transform will be matched with partners where problem statements can be identified, solutions discussed, and relevant upskilling programmes matched.
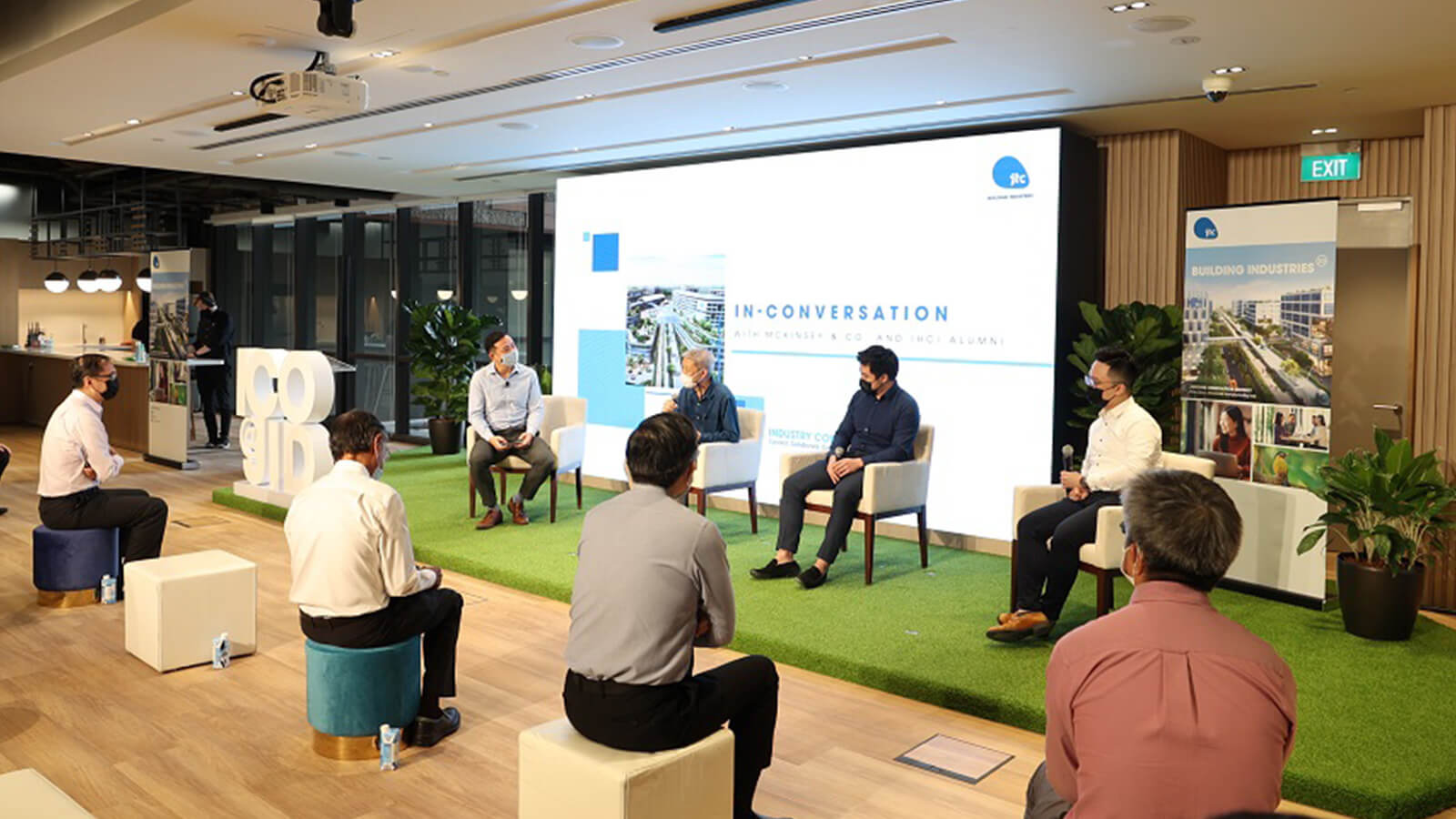
Under the Singapore Business Federation’s I4.0 Human Capital Initiative Enabler Programme, we also have more than 10 Community of Practice partners such as Siemens and Bosch Rexroth come together to help interested companies with the scaling and deployment of Industry 4.0 solutions. This forms part of the continual support structure put in place to uplift businesses and reach the intended outcomes. In the meantime, we are also creating platforms and formalising partnerships to advance sustainable manufacturing in Singapore and Asia.
This is an exciting journey that we at JTC have embarked on, and one we are committed to continuing. At JID, we are laying the foundations and the building blocks necessary so that we can write the new chapters of manufacturing’s future. We welcome businesses to join us on this path.
This article is reproduced from Mr Tan Boon Khai’s keynote sharing at Industrial Transformation Asia Pacific 2021.