Since 2015, Nanyang Technological University (NTU) and JTC have been working together to develop two robots – QuicaBot and PictoBot - for use in the construction industry.
QuicaBot – short for Quality Inspection and Assessment Robot – can be used to check defects in buildings, picking up non-conformance such as cracks, uneven surfaces and walls meeting at angles that are out of square.
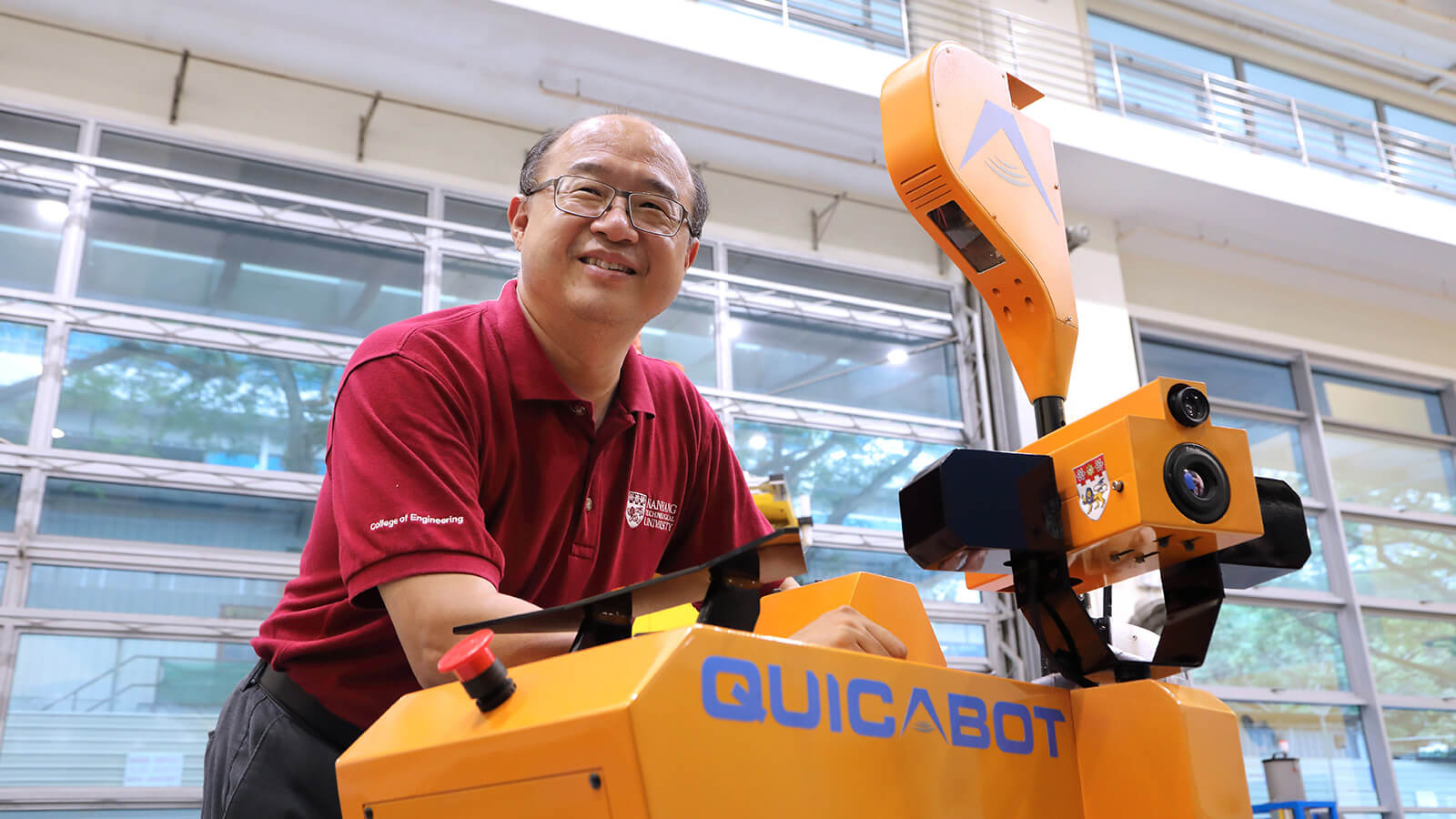
When human inspectors are checking whether walls meet at right angles and if floors are even, they use tools such as set squares and spirit levels. QuicaBot uses a laser scanner to capture 3D data of the room to check if the walls are properly aligned and even. QuicaBot also uses an inclinometer to check the slope of floors, a visual camera to pick up cracks in the building and a thermal infrared camera that uses heat to detect hollowness and hollow tiles.
It usually takes two human inspectors a day to finish inspecting a building. With QuicaBot, only one human inspector is needed and the inspection will only take half a day. QuicaBot can also inspect the building with greater accuracy and consistency than a human inspector. The robot can upload its 3D data into a database, meaning that all detects will have their locations, visual and detailed measurements recorded automatically. Data in the cloud can be directly accessed by builders and developers.
According to Professor Chen I-Ming, Director of the Robotics Research Centre at NTU’s School of Mechanical & Aerospace Engineering, and Co-Thrust Leader (Infrastructure Systems and Materials), JTC came to him with a real-world problem in the construction industry and challenged his team to come up with a solution. Since the beginning of the project in 2015, NTU worked with JTC’s experienced engineers and management to support the progress of the robot. “JTC gave us lots of feedback,” said Professor Chen. “They provided us with domain knowledge and helped us refine the features of the robot. When inspecting a building, there are many items we needed to check – BCA has a 70-page manual for this – so we had to figure out which can be done better by a human and which by a robot.”
It’s a challenge finding a building that fits into that time. By testing the robot at a building with completed Architecture works like JTC Space @ Gul, we can test the robot all year round instead of having to wait for a different building to be ready every time.
When Professor Chen showed the robot to people in the construction industry, he received a positive response. “The industry people think this robot is very relevant. This project is different from some of our other projects, which is less applicable to industry.”
Professor Chen has been working with JTC since 2014, a partnership that naturally progressed from a National Research Foundation (NRF) task force created to address the problem of labour shortage and rising labour costs in the construction industry. “The construction industry is a very critical sector in Singapore and we held a workshop with JTC to look into this area. So our collaboration came at the right time, since we were both interested in solutions to enhance the productivity of the construction industry.
NTU plans to test QuicaBot at JTC Space @ Gul. “For this type of robot, you use it only at a very specific time, which is after completion of the Architectural works of a building as a prerequisite prior to obtaining TOP (Temporary Occupation Permit) or CSC (Certificate of Statutory Completion),” said Professor Chen. “It’s a challenge finding a building that fits into that time. By testing the robot at a building with completed Architecture works like JTC Space @ Gul, we can test the robot all year round instead of having to wait for a different building to be ready every time.”
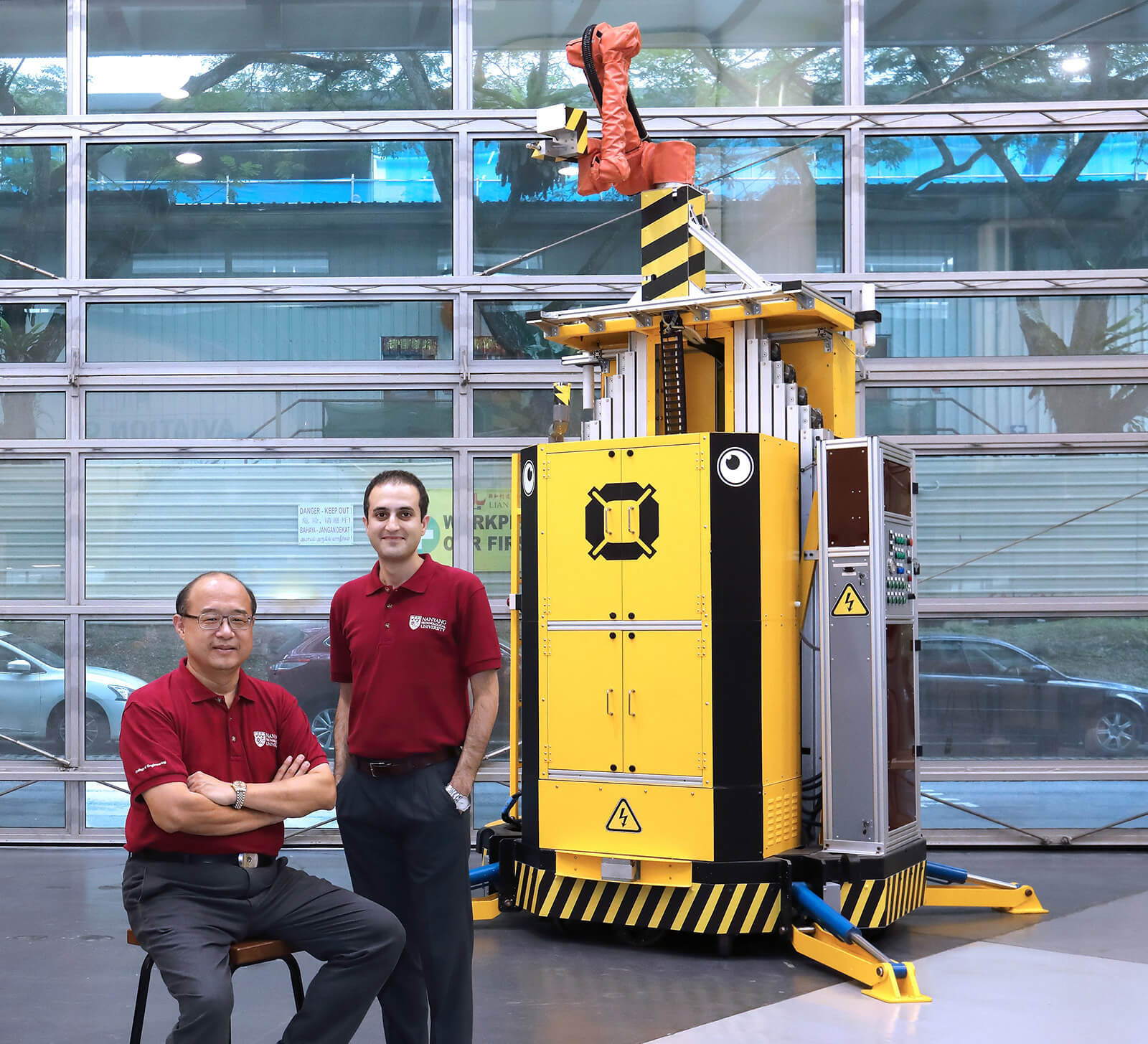
Professor Chen says the next step for QuicaBot is to figure out how to commercialise the robot. “We also want to enhance its capability to check for more types of defects, such as leakage and uniformity of the colour or the paint,” he says.
The other robot that NTU and JTC is working together on is PictoBot, which can paint walls and ceilings up to 10 metres in height, making it ideal for industrial buildings.
PictoBot automatically scans its surroundings and navigates walls using an optical camera and laser scanner, moving up and down via an automated jack-up platform, while spray-painting the walls with its six-axis robotic arm.
Industrial buildings usually have high ceilings, which means that human painters are exposed to various safety risks while doing their job. PictoBot can paint a wall 25 per cent faster than a crew of two painters, thus improving productivity and safety. PictoBot can also be used in the dark, enabling 24-hours continuous painting.
Professor Chen said that JTC provided his team with useful feedback, including inputs and requirements from the perspective of the industry when they were designing the robot. “JTC helped us improve the accessibility of the robot to the places it is designed to be used. For example, things like making sure that the robot could go through the door and fit into a lift. These are basic requirements but sometimes we can forget.”
Future steps for the development of PictoBot include creating a smaller version which can be used in offices and residences. “We’re also thinking of how we can use PictoBot for cleaning, designing it to spray water. If we can use the same robot to do different types of work, that would add more value to our product,” said Professor Chen.