For the longest time, plastic waste has been regarded as a bane for the environment. But what if we were to unlearn what we know about plastic waste, and instead regard it as a potential resource? Around the world, researchers are already seeing it in a different light — they are giving this non-biodegradable material a second life by recycling it.
Here in Singapore, a JTC-led research team is studying the feasibility of substituting natural sand in concrete for recycled plastic waste. The results have been promising, bringing us closer towards a circular economy for plastics. Senior engineer Mr Kevin Emanuel Suhartono shares more.
Let’s get down to the nitty-gritty of this eye-opening project. What is it about?
This project began in 2020. It is a collective effort by JTC, National Environment Agency (NEA) and Temasek Polytechnic (TP), and the project idea was submitted to the Engineering Innovation Challenge organised by the Public Sector Science and Technology Policy and Plans Office (S&TPPO). We explored how recycled plastic waste can be turned into a fine aggregate alternative for use in concrete. After a year or so of experimentation, we have developed a plastic-concrete formulation that calls for replacing 20% of its sand volume with recycled plastic waste. Once cured, the alternative concrete can be used for non-structural elements.
What are non-structural elements, and what applications is the mix being used for?
Generally, the construction industry classifies elements into structural and non-structural. Within a building, structural elements are the load-bearing walls, columns, beams, floors, and foundations. Non-structural elements are not intended to support any loads, at least not for extended periods of time.
We explored the feasibility of using the plastic-concrete mix to make road kerbs, which are edge dividers that prevent motorists from driving on to pavements. Based on the results of our laboratory tests, we found that the physical and mechanical properties of the plastic-concrete mix are comparable with those of conventional concrete. Then, we consulted the relevant authorities and received the green light as well as support to deploy our prototypes at an infrastructure project near Tuas Link MRT station, where JTC is currently constructing a road, along with a roadside drain, sewer line, and footpath. Their performance has been encouraging thus far.
Where else can the plastic-concrete mix be used?
Another application is drain channels. Our experiments have revealed that the properties of conventional hardened concrete used for drain channels do not differ much from our mix’s. However, it is important to assess the environmental impact of our plastic-concrete applications, since with the use of plastics comes the risk of leaching. Leaching happens when chemicals from the plastics leak and penetrate into the surrounding environments. This is an essential consideration for drain channels because the rainwater that comes into contact with them will return to the reservoir, and eventually be treated for daily use.
This is where our partners from NEA have been a great source of help, as they provided sound advice on mitigating plastic leaching. We have run several laboratory experiments on collected samples of surface run-off water, and the results have also been optimistic. But of course, further onsite monitoring over longer periods of time will need to be conducted to ensure the risk of leaching is eliminated.
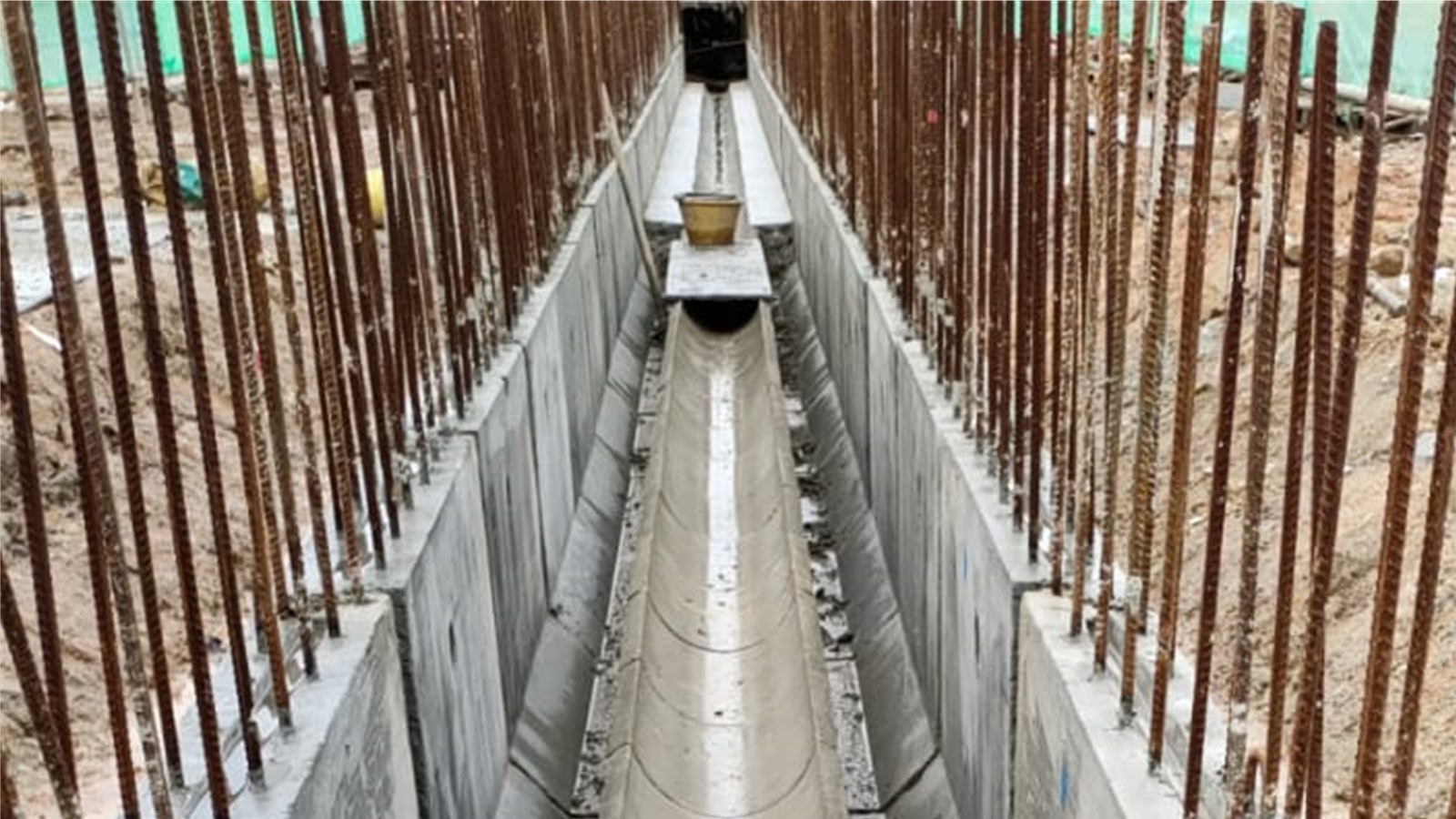
Take us through the crystallisation of this project idea.
As a starting point, the team thought about the practical uses of recycled plastic waste. For JTC team members, our thoughts naturally turned to the pressing issues the construction industry faced. The volatile supply of raw materials is one. Right now, Singapore imports most of its raw materials from other countries. There is a need for us to examine how we can process materials readily available on our shores, and use them to create valuable resources. This will in turn enhance the resilience of our construction industry.
We identified concrete as one of the most in-demand construction materials. We then toyed with the idea that recycled plastic waste could be used to replace the ingredient of sand. Our project is in fact a riff on the works of other researchers, who had already been investigating the use of plastic waste in concrete. Their research, however, focused more on the strength performance of alternative concrete — for us, we wanted to go a step further, and find actual applications for it.
Why is sand, out of all the other ingredients used to make concrete, suitable for replacement?
Concrete is a composite material made up of four main ingredients: water, cement as well as aggregates such as sand and gravel. Water cannot be taken out of the equation, as it is required to wet the surfaces of the ingredients so that they form an adhesive quality. Moreover, it is of a completely different state from plastics. Cement is like the glue — during the hydration process, it reacts with water, then adheres to the aggregates, and binds them. That leaves us with sand and gravel.
Both aggregates affect the concrete’s compressive strength, which is its resistance to break when withstanding loads. The chief difference between the two is particle size. Sand grains are very fine, ranging from 0.1mm to 2mm, whereas gravel sediments are coarser and larger, measuring from 4.75mm upwards. Our hypothesis is that given today’s technology, the strength of recycled plastic waste will not match that of gravel. Hence, sand was the more viable option for replacement.
And what makes plastics an ideal substitute for sand, given that they are apples and oranges by comparison?
Plastics have an inherent durability. Despite their lower strength as compared with natural aggregates’, they do possess good hardness in general. The hardness of the natural aggregates is very important, as it contributes to the overall performance of the produced concrete once it is cured. Using recycled plastic waste as an alternative aggregate would indeed yield a reduction in the cured concrete’s compressive strength. Hence, it is critical for us to determine the optimal replacement percentage of sand for plastics , depending on the intended application, to strike a balance.
How is the plastic waste processed, and then used in the formulation?
The plastics, when they reach the recycling company that we work with, are in their original forms: bubble tea cups, water bottles, grocery bags, and the likes. The company will process the waste into plastic sheets, which are then sent over to TP. At TP’s laboratories, the sheets are further pulverised into pellet-sized particles that measure about 2mm to 4mm. The particles are then ready for use in the formulation.
Working alongside our partners, JTC provided our technical inputs and design perspectives, while TP came up with the formulations to meet the unique specifications of our road kerbs and drain channels. We underwent iterative testing by varying the sand-replacement volume in multiple concrete specimens, before finally deriving the optimal ratio.
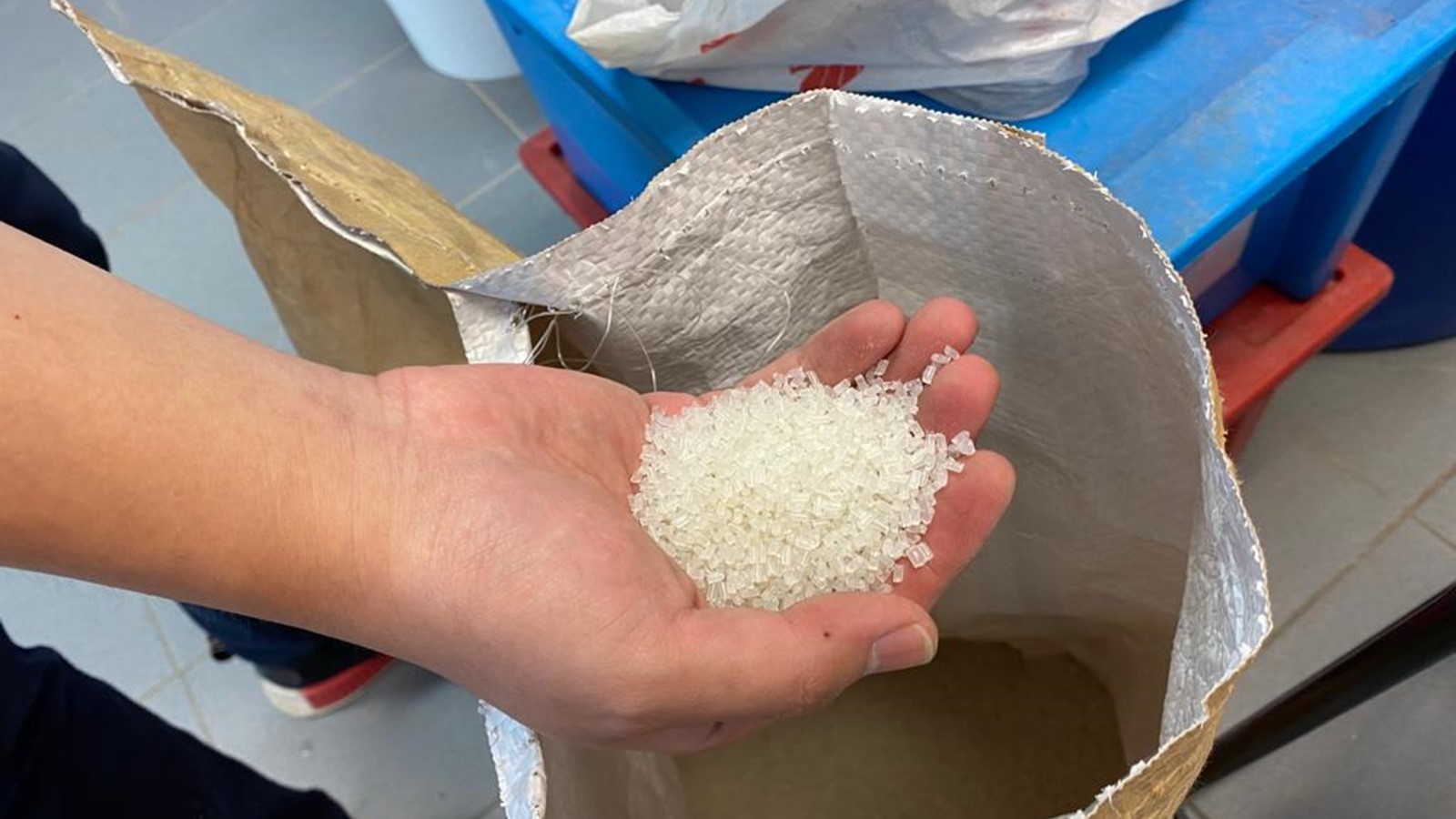
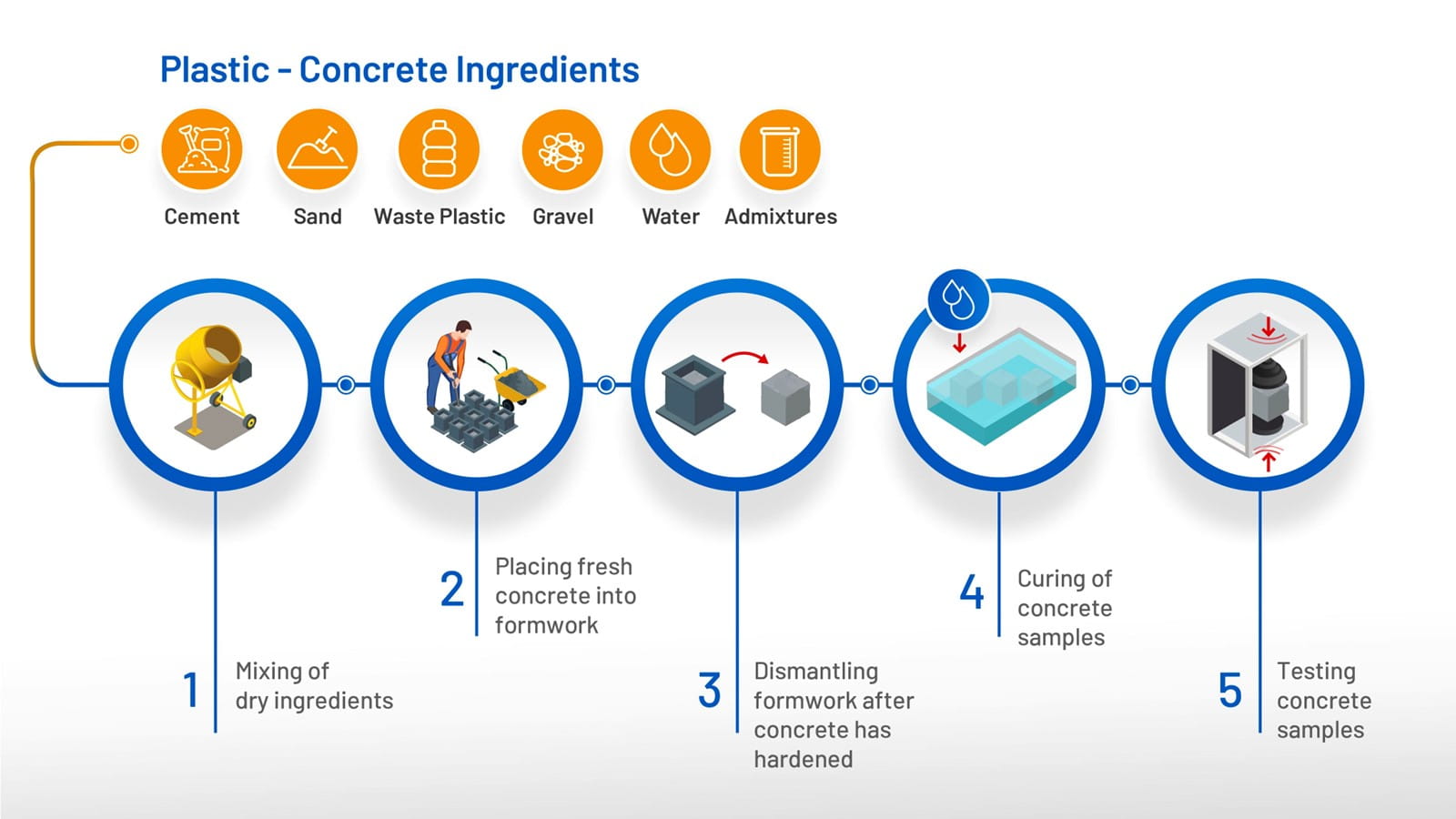
Research journeys are often long and may even be frustrating. What
was the process like for your team?
Frankly, it was quite stressful at the beginning. We had the central idea, and we knew the objectives we wanted to achieve. But how to get to the goal was a huge question mark. There were no standards or codes on plastic-concrete design for us to refer to. Once we had achieved the ideal formulation after much trial and error, we began brainstorming prototype ideas. Being mindful of the EIC’s tight project timeline, we did not want to shoot for the moon and produce prototypes so novel that obtaining approval from the authorities to install them would be challenging. The sensible thing was to design an easy-to-produce solution, yet one that would be widely used by industry players.
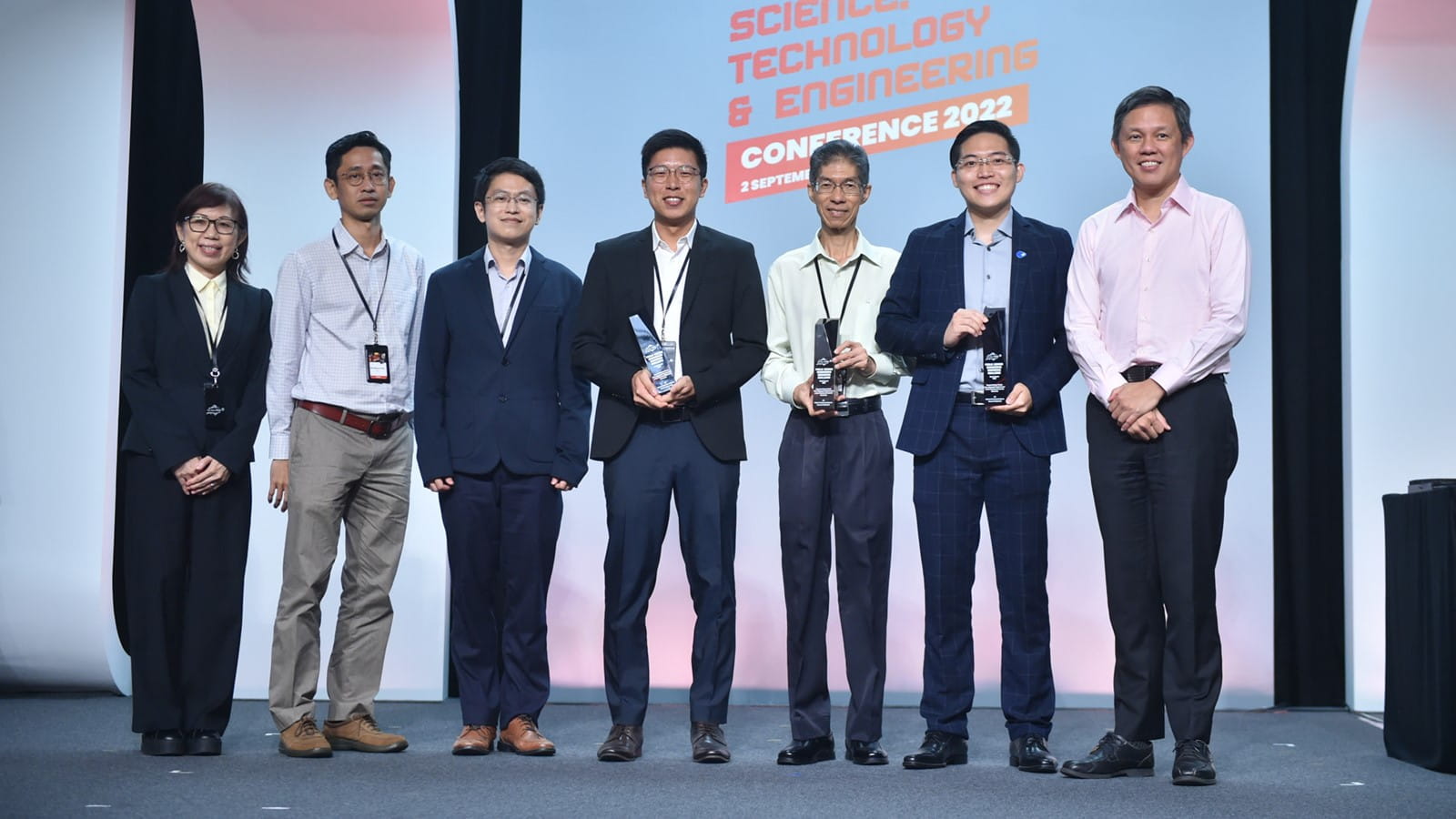
What do you do when you get stuck? Always go back to the end-users. Our JTC team members began reaching out to specialists in precast concrete works and conducted market surveys. From their responses, we identified about six widely used non-structural elements, which were eventually narrowed down to road kerbs and drain channels.
As the plastic-concrete mix is a novel product, how likely is its adoption
by Singapore’s construction industry?
Cost is always a major consideration for construction businesses,
as they want to protect their profit margins. If using sustainable materials means
incurring higher costs, then there will likely be an inertia to make the switch.
Hence, we are looking at ways to bring down the price tag of the
plastic-concrete mix. Plastic waste as a resource is, in a sense, “free”; the
cost comes from treating and downsizing it to become sand-like particles. The
status quo is that there are not many players in Singapore who specialise in this
craft. Also, because we are currently producing the mix in small batches, we do
not yet enjoy economies of scale.
Furthermore, before we can introduce it for industrywide adoption, new standards and codes will need to be rigorously studied and developed. While it is the team’s hope that it will eventually be used for structural elements, we certainly do not want to rush into it. As civil engineers, we are dealing with people’s lives when we design and construct buildings, and the slightest building damage can lead to catastrophic consequences. More studies will have to be conducted to verify that the performance of this “green” concrete is indeed adequate before it can be used to produce structural elements.
For now, we have started small and will strive to deliver broader applications. Like I said, the results of our experiments have thus far been positive. As we continue to deploy it in more trials and infrastructure projects, our confidence about its performance and suitability for industry use will steadily grow.
A childhood fascination with numbers led Mr Kevin Emanuel Suhartono to pursue a career in civil engineering. In his previous appointment as a senior engineer in JTC’s Technical Services Division, he oversaw building and infrastructure development projects. The Indonesian-born individual is hugely passionate about sustainability, and actively spearheads relevant projects such as research for an innovative plastic-concrete mix as well as solar deployment on building rooftops across JTC estates. He is now with JTC’s Sustainability Department.